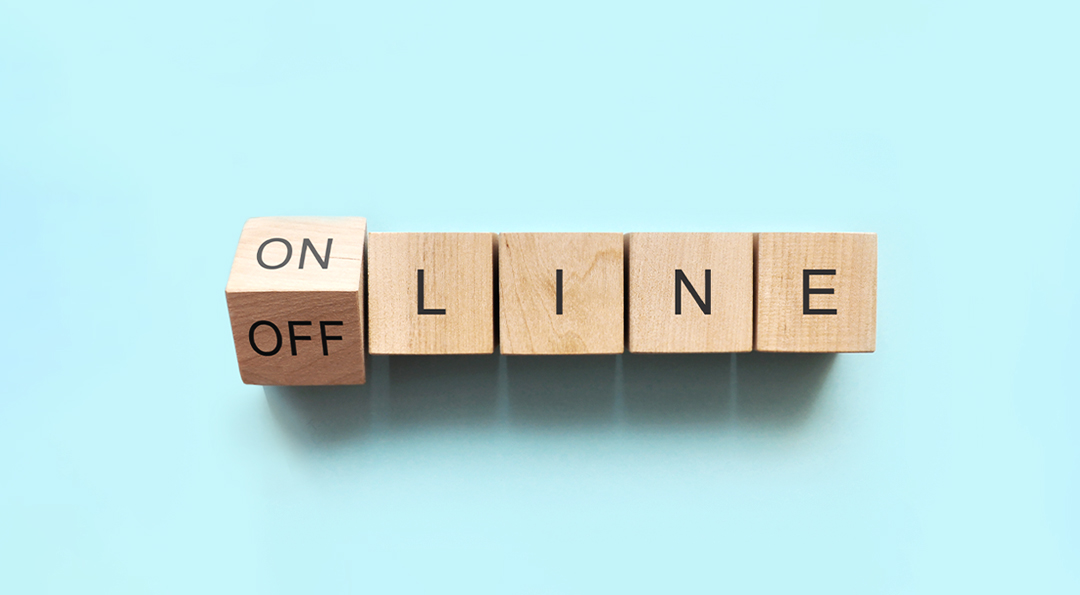
최근 불어오는 DX 열풍의 핵심, 온·오프라인 통합
최근 전 세계적으로 DX가 뜨겁게 주목받는 이유는 날이 갈수록 치열해지는 제조업 경쟁 속에서 새로운 제조 혁신이 필수적으로 요구되기 때문입니다. 그리고 그 제조 혁신의 중심에는 DX가 자리잡고 있죠. 제조업의 혁신 과정을 이끌어줄 디지털 기술에 대한 요구가 최근 크게 증가하고 있으며, 전통적인 오프라인 제조에서 벗어나 제조업의 패러다임을 바꿀 수 있는 디지털 데이터 활용에 대한 관심 또한 나날이 높아지고 있습니다. 이러한 디지털 데이터를 활용한 DX만이 경쟁에서 살아남을 수 있는 게임 체인저급 혁신이 될 수 있는 것이죠.
특히, 요즘 디지털 트랜스포메이션은 단순히 온라인 또는 오프라인 한 곳에 집중되어 나타나지 않고 온·오프라인 모두를 통합해 나타나는 것이 특징입니다. 현재 어느 한 쪽으로 치우쳐진 DX 혁신만으로는 분명한 한계가 있으며, 진정한 제조업의 DX 혁신을 이룩하기는 어려운 상황이죠. 이 때문에 많은 기업들이 온라인과 오프라인을 동시에 혁신하는 통합적 DX를 실천하고자 노력하고 있습니다.
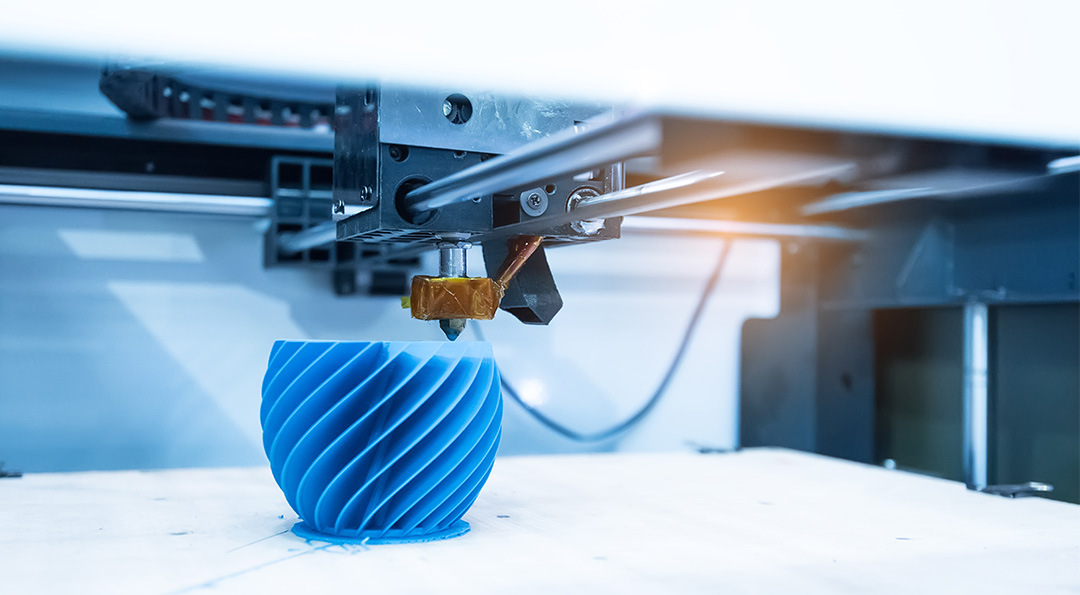
보잉의 항공우주 제조 혁신에 3D 프린터가 사용되는 이유
보잉의 혁신적인 첫 번째 디지털 트랜스포메이션은 바로 3D 프린터를 활용한 스마트 팩토리 혁신입니다. 보잉은 오래 전부터 3D 프린팅 기술 도입을 추진해왔는데요. 2015년에는 3D 프린트 항공 부품에 대한 특허를 신청하기도 하였고, 2016년에는 3D 프린터 제조업체 스트라타시스(Stratasys)와 함께 탄소섬유 같은 소재를 사용해 거의 모든 크기의 물체를 더 가볍고 강하게 출력하는 산업용 3D 프린터를 테스트하였습니다. 3D 프린팅은 제작 비용과 동체의 무게를 줄이고, 여러 개의 개별적 구조 부품을 구별 없이 하나로 통합이 가능해 통합 구조로 설계, 생산할 수 있다는 점에서 제조업에서 아주 혁신적인 기술로 불리죠.
현재 보잉은 3D 프린터를 활용해 787 드림라이너(Dreamliner) 항공기에 대당 적어도 4개의 3D 프린트 티타늄 부품을 사용하고 있는데요. 앞으로 보잉은 비행기 설계에 겹겹이 쌓아 제조하는 적층제조(additive manufacturing)를 통해 3D 프린팅 부품을 1,000개까지 늘릴 예정입니다. 만일 1,000개 이상의 3D 프린팅 부품이 사용된다면 매년 144대의 드림라이너를 생산하는 보잉은 제조 비용을 대당 300만 달러까지 절감시킬 수 있다고 하죠.
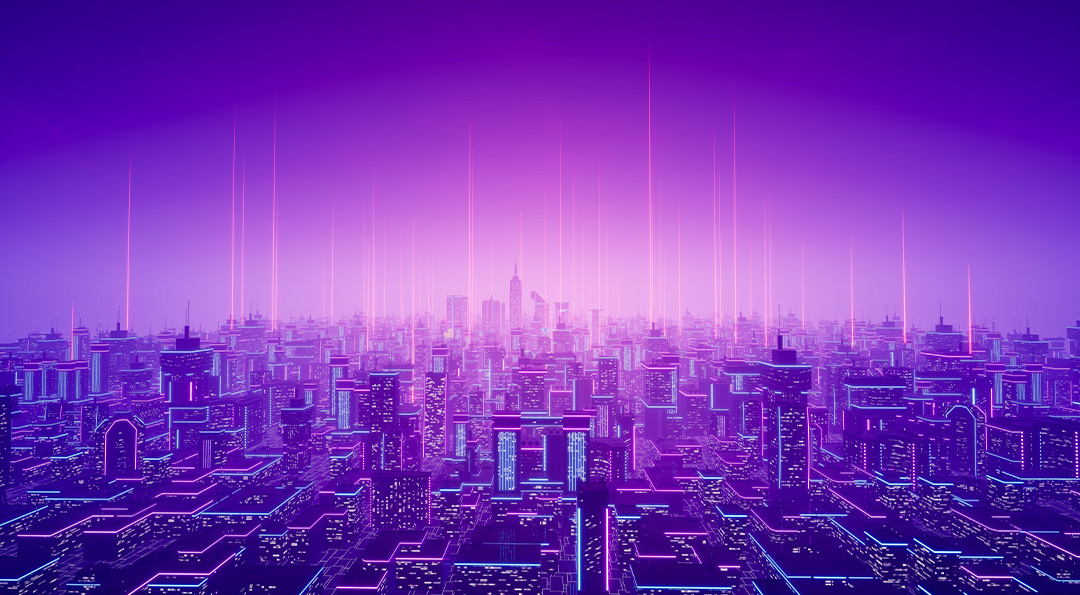
메타버스를 활용한 ‘보잉’의 온라인 DX 혁신
보잉이 선보이는 또 하나의 DX는 다름아닌 디지털 데이터를 활용한 ‘온라인 DX’입니다. 보잉은 차기 새 항공기의 제조 과정 및 실제 운행을 테스트하기 위해 가상 공간, 즉 메타버스(Metaverse)를 활용하고 있는데요. 제트기와 생산 시스템의 가상 3차원인 ‘디지털 트윈(Digital Twin)’를 만들고, 모든 디지털 트윈의 기능을 연결하기 위한 디지털 스레드(Digital Thread)를 활용하여 설계부터 유지까지 제조업 전 과정에 혁신을 일으키고 있습니다.
실제로 보잉은 이 ‘디지털 트윈 자산 개발 모델’을 사용하여 산업용 및 군용 항공기 제조에 사용하는 부품 및 시스템의 초기 품질을 최대40%까지 개선할 수 있었으며, 보잉사의 CEO 데니스 뮐렌버그는 “이 디지털 트윈 기술은 향후 10년동안 세계 최대의 비행기 제조사에 있어 생산 효율 향상의 가장 큰 원동력이 될 것”이라고 말했습니다.
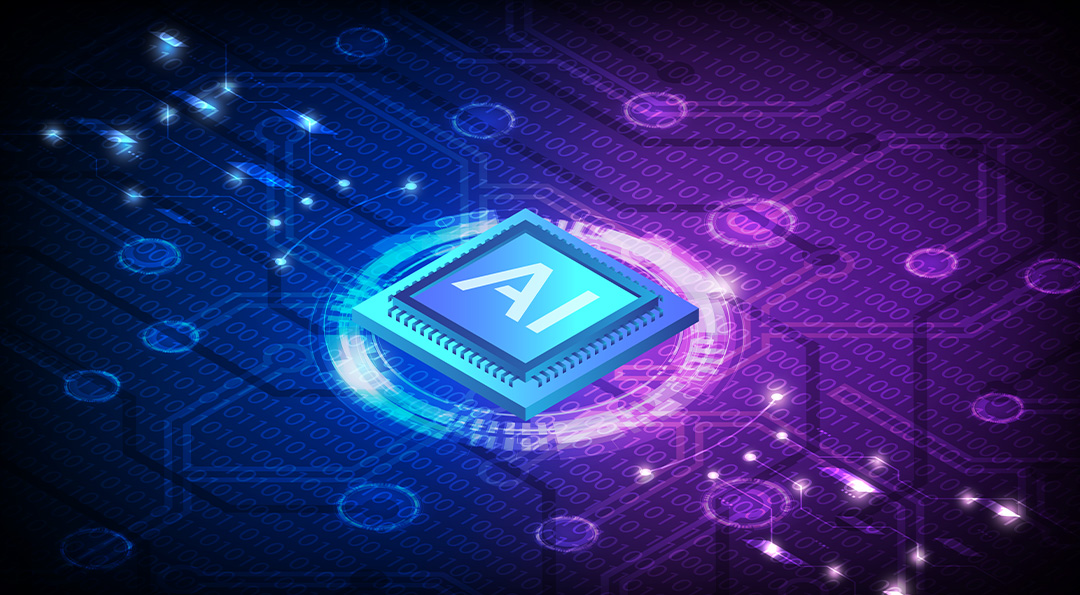
클라우드와 AI를 활용한 ‘보잉’의 디지털 트랜스포메이션 가속화
보잉은 우선 여러 비즈니스 그룹에 걸쳐 모든 데이터를 구글 클라우드로 이행시킬 계획인데요. 관련 모든 데이터를 클라우드에 입력하고 이를 유연하게 확장함으로써 사내 전체에서 공유될 수 있는 데이터허브를 만들고 있습니다. 이러한 통합적 데이터는 문제점에 대한 해결책을 찾는 통합적인 사고를 가능하게 만든다는 점에서 그 의의가 크죠. 또한 통합적인 데이터를 모두가 확인할 수 있다는 점에서 각 부서들의 커뮤니케이션 및 생산성 향상에 있어서도 의미가 있다고 할 수 있습니다.
또한 보잉은 애저, 코타나 인텔리전스(Cortana Intelligence) 등 클라우드와 인공지능 솔루션을 기존 시스템에 접목하였는데요. 코타나 인텔리전스는 클라우드 상에서 제공되는 빅데이터, 머신러닝, 인지, 분석 및 지능봇 등을 구현할 수 있도록 해주는 솔루션으로 머신러닝 알고리즘을 기반으로 경고 및 추천하는 행동들을 고려해 보다 나은 의사 결정을 내릴 수 있으며, 이러한 의사 결정 과정을 자동화함으로써 보다 효율적인 운영이 가능하도록 도와줍니다. ‘보잉’은 이러한 기술들을 활용해 보다 신속한 소프트웨어 변경이 가능해졌고 실시간으로 기계 정보를 수집, 분석하며 항공기 유지보수에 대한 시기 및 정보를 예측하고, 연료 효율을 최적화함과 동시에 조종사, 엔지니어, 승무원 등 더 효율적으로 비행 업무를 할 수 있게 지원하는 등 다양한 방면에서 혁신을 일으키고 있습니다. 이렇듯 ‘보잉’은 클라우드와 AI를 활용해 지속적인 혁신을 이룰 수 있는 DX를 추진하고 있습니다.
제조업 혁신을 위해 필수적인 디지털 트랜스포메이션
제조업에 있어서 업무 개선 및 효율 증대를 위한 디지털화는 필수적이며, 이는 온·오프라인을 가리지 않고 연달아 나타나고 있습니다. 앞서 말했듯, 이렇게 빠르게 변화하는 흐름에서 뒤쳐지지 않기 위해서는 DX를 활용해 기존에 불가능했던 새로운 혁신을 일으켜야 하며, 온라인 혹은 오프라인 한 곳에만 국한된 것이 아닌 통합적 DX를 통해 그 시너지 효과를 키워야만 합니다.
GS칼텍스는 앞서 이야기한 ‘보잉’과 마찬가지로 변화하는 제조업 환경에 맞춰 클라우드 기반의 전사 데이터 허브를 구축하고 있으며, 이를 바탕으로 데이터 기반의 의사결정을 강화하고 업무효율성을 개선시키고 있습니다.
또한 3D 공간인 디지털 트윈을 구축하여 다양한 상황을 시뮬레이션하고 최적의 운영 방안을 검토해 공장 운영의 효율을 높이는 등으로 온라인 디지털 트랜스포메이션을 적극 진행하고 있습니다. 2019년, 여수공장에서는 3D(3차원) 모델을 통해 설비의 모든 데이터를 쉽게 찾을 수 있는 시스템을 제3고도화시설(VRHCR) 공정에 적용해 설비와 관련된 정비 이력, 도면 등 데이터를 찾는 시간이 이전보다 30%가량 줄였고, 또 현장 구조물 설치 등 공간 확인이 필요한 작업 때도 현장에 직접 가지 않고 3D 모델로 확인함으로써 소요시간이 약 70% 줄어드는 등 DX를 활용해 기존에 없던 혁신을 불러일으키고 있습니다.
앞으로도 GS칼텍스는 전사적인 DX 활동을 통해 급변하는 미래 환경에 효율적으로 빠르게 대응하고 기업의 경쟁력을 높일 수 있도록 노력할 것입니다.