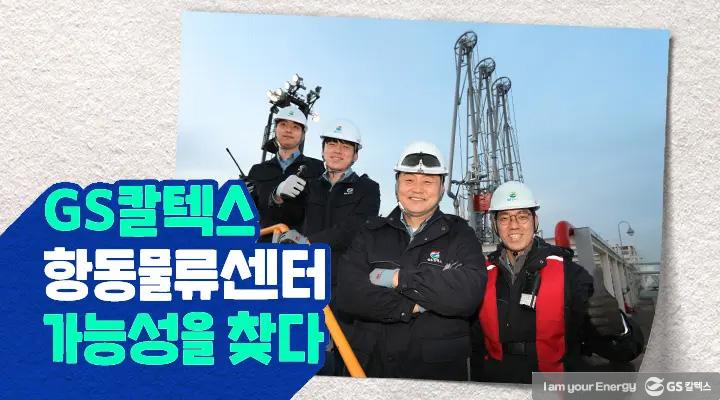
많은 사람들은 기존 경험과 지식을 바탕으로 문제를 해결해 나갑니다. 하지만 기존의 관행, 경험, 노하우, 지식이 때로는 문제 해결을 방해할 때가 있습니다. 그럴 때 필요한 것이 바로 제로베이스부터 검토하는 노력이죠. 기존 경험에서 탈피하고 문제를 새로운 시각에서 다시 본다면 새로운 변화를 이끌어 낼 수 있습니다. 최근 GS칼텍스 항동물류센터 구성원들이 제로베이스부터 검토하여 업무 효율성을 증대하고 Risk를 개선한 사례가 있다는 소식이 도착했습니다. 자세히 알아볼까요?
로딩암 3기 동시 입고를 통해 ‘업무 효율화+사고 예방+비용 절감’ 세 마리 토끼를 잡다
‘유휴’의 의미는 쓸모 없는 것이 아닌 사용하지 않는 것을 의미합니다. 그렇기 때문에 유휴 시설은 충분히 새로운 가능성을 가지고 활용될 수 있는 것이죠. 항동물류센터는 기존 SK가 운영하던 시설을 2019년 7월 GS칼텍스가 일부 인수하여 운영하기 시작한 곳입니다. 항동물류센터는 총 3기의 로딩암*[efn_note]로딩암(loading arm) : 석유화학제품을 하역하거나 선적할 때 사용되는 배관 설비[/efn_note] 중 휘발유/경유 전용으로 1기, 항공유 전용으로 1기로 2기만 사용하고 있었는데요. 나머지 1기의 로딩암은 인수 전 벙커유 전용으로 사용되었기에 유휴 시설로 분류되어 미사용 중이었죠. 2020년 항동물류센터에서는 유휴 시설인 로딩암 1기에 대한 활용 방안을 제로베이스에서부터 고민하게 되었습니다.
문제점 마주하기
2기의 로딩암을 운전하고 있는 상황에서 발생 가능한 문제점부터 상세하게 파악했습니다. 첫째, 휘발유와 경유가 같은 로딩암을 사용하기에 선박 입고 작업 시 다양한 리스크가 존재합니다. 유종 변경을 위해 로딩암 탈부착 시 협착, 화재/폭발, 유출 사고 발생 가능성이 있죠. 또한 제품 간 혼유 사고도 발생할 수 있습니다. 둘째, 미사용 중인 1기의 로딩암은 사용 시에만 식별 가능한 결함 사항 파악이 어렵다는 점과 더불어 유지 보수가 힘들기에 노후화가 빠르게 진행된다는 단점이 있었습니다. 마지막으로, 현재 사용 중인 로딩암이 고장 난다면 수리가 완료될 때까지 해당 로딩암을 통해 입고되는 유종에 대해서는 작업이 불가능하다는 것이었죠.
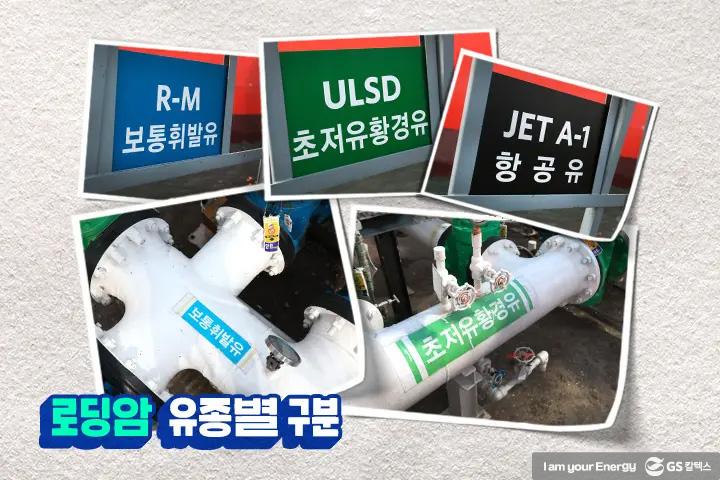
가능성을 현실로
다양한 문제점을 개선하기 위해 항무사, 운영해운, 교대조 모두가 하나되어 지속적으로 파일럿 테스트를 진행했습니다. 또한 개선한다면 기대되는 효과, 개선 과정에서 발생할 수 있는 잠재 위험성에 대해서도 함께 검토하는 과정을 거쳤죠. 2020년 하반기, 수 차례 테스트를 진행하여 올해부터 로딩암 3기 동시 입고가 가능해졌습니다. 그 결과 첫째, 휘발유/경유/항공유를 단독 로딩암으로 구성하고 3기 동시 입고 작업을 진행하여 코리아비너스호 선적량이 증대될 수 있었습니다. 해당 선적의 유창(기름 창고) 허용량을 파악하여 최대 입고량을 토대로 효율적인 선박 입고가 가능하도록 개선된 것이죠. 둘째, 유종별 개별 로딩암 사용으로 인해 혼유 사고, 협착, 화재/폭발, 유출 등 안전 사고 예방은 물론 품질에 대한 Risk 해소도 가능해졌습니다. 마지막으로 교대조 운영 업무 중 불필요한 loss를 제거하여 업무 효율성 증대는 물론 비용 절감까지 이뤄냈습니다.
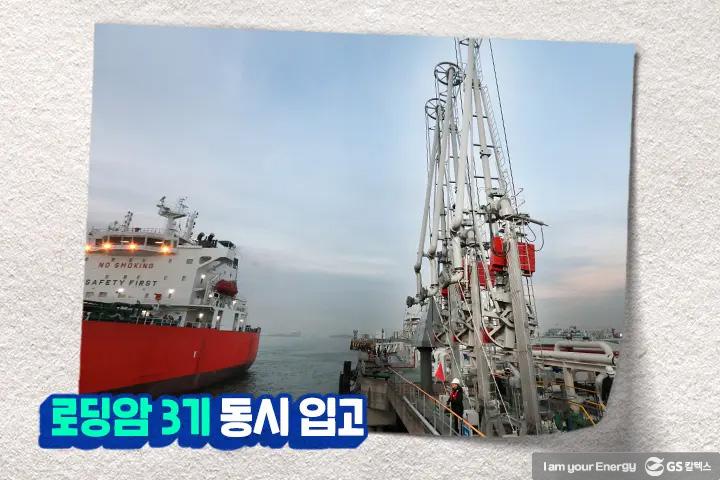
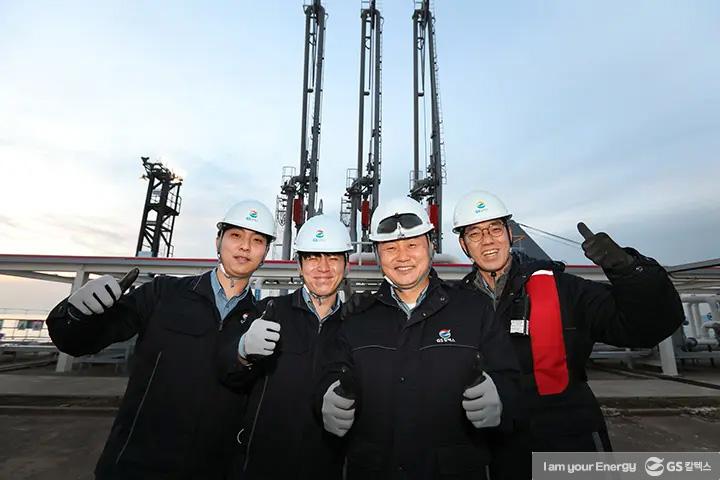
송유펌프 임펠러 교체를 통해 송유 출하 효율성을 증대시키다
제로베이스부터 다시 검토하여 개선하고자 한 사례는 GS칼텍스 항동물류센터에 또 있었습니다. 기존 설비/운전 조건에서 목표치 달성은 어려운 상황이었지만 다양한 시도를 통해 끝내 송유량 증대를 이뤄낸 사례입니다.
현황 파악을 통해 개선 방향 찾기
GS칼텍스 항동물류센터에서 인천에 위치한 공항으로 항공유를 옮기는 방법은 단 한가지 입니다. 바로, 파이프라인을 통해서 송유가 이뤄지죠. 따라서 물류센터에서 공항까지 이어진 약 40km의 파이프를 타고 항공유가 이동하기 위해서는 펌프의 압력이 매우 중요합니다. 하지만 항동물류센터는 노후화된 시설로 인해 압력을 무작정 높일 수만은 없는 상황이었죠. 그래서 제로베이스부터 시작하여 설비 현황부터 파악했습니다. 기존 배관 데이터의 오류를 발견하고 6가지 케이스로 가설을 수립하여 최적의 운전 조건도 검토했죠. 그 결과, 펌프 날개라고 불리는 임펠러 단수를 2단(stage)에서 3단(stage)으로 교체하는 개선 방향을 찾아낼 수 있었습니다.
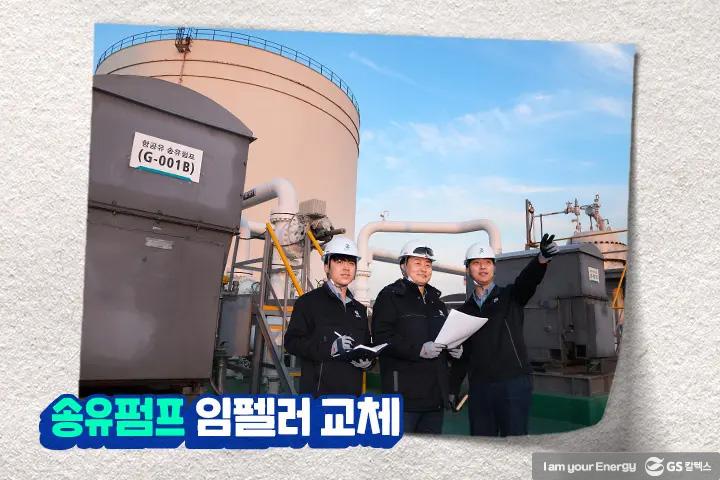
기대 이상의 목표를 달성하며
임펠러 3단(stage) 교체를 통해 펌프 2기를 운전하는 경우, 유량을 평균 800m3/h에서 평균 1,000 m3/h까지 증가시킬 수 있었습니다. 즉, 송유량 증대는 물론 송유 시간 단축도 가능해진 것이죠. 항동물류센터는 한 단계 더 나아가 교체 과정에서도 더 나은 방법을 고민했습니다. 펌프 부품을 꼼꼼히 비교하여 납기 시간을 단축하고 교체도 용이한 저비용의 국산 부품으로 대체했습니다. 외산 제품보다 3배 가량의 투자비를 절감할 수 있었죠.
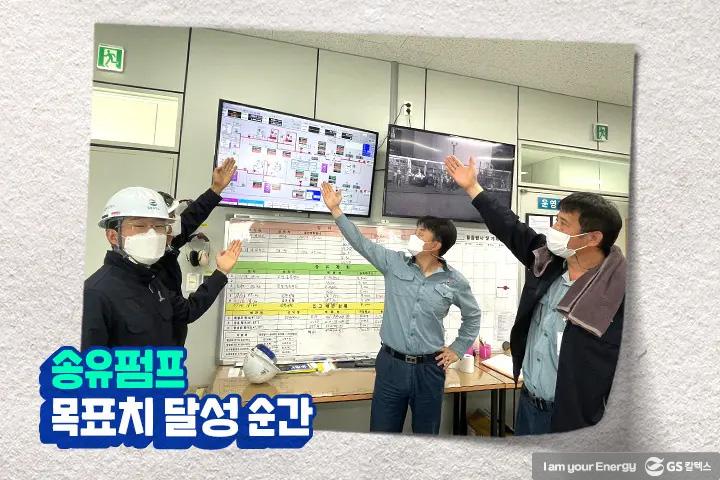
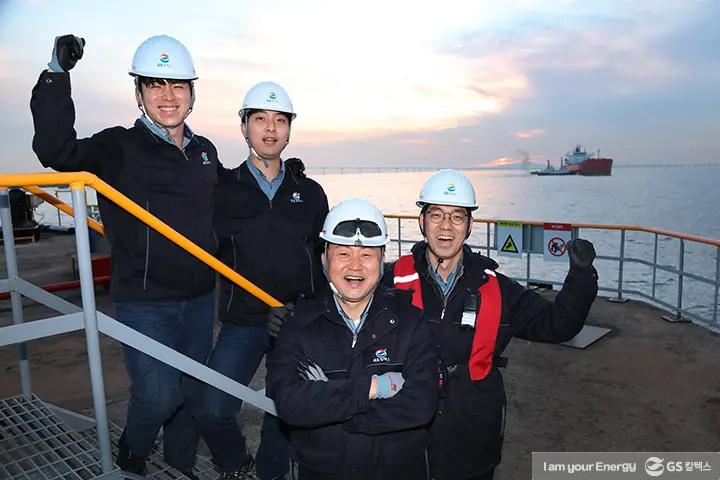
개선을 위해 노력한 GS칼텍스 항동물류센터 주인공을 만나다
예상되는 리스크를 감수하고서라도 개선을 위해 지속적으로 노력한 이번 사례 주인공들을 만나보았습니다. 그들의 생생한 후기를 들어보시죠.
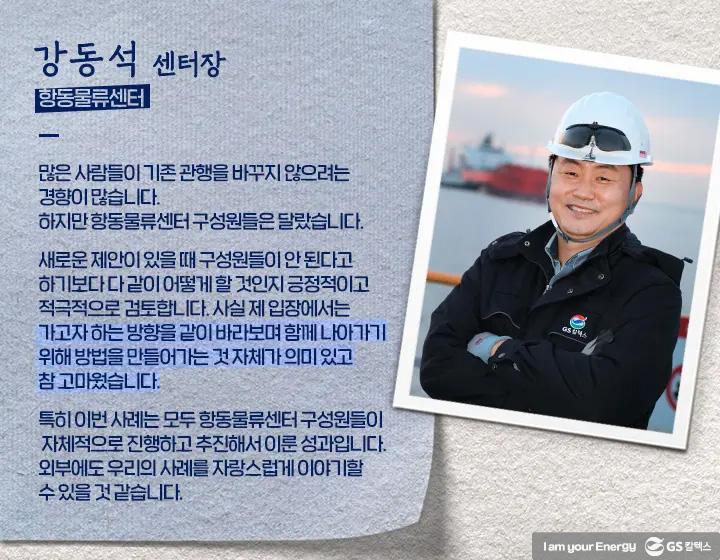
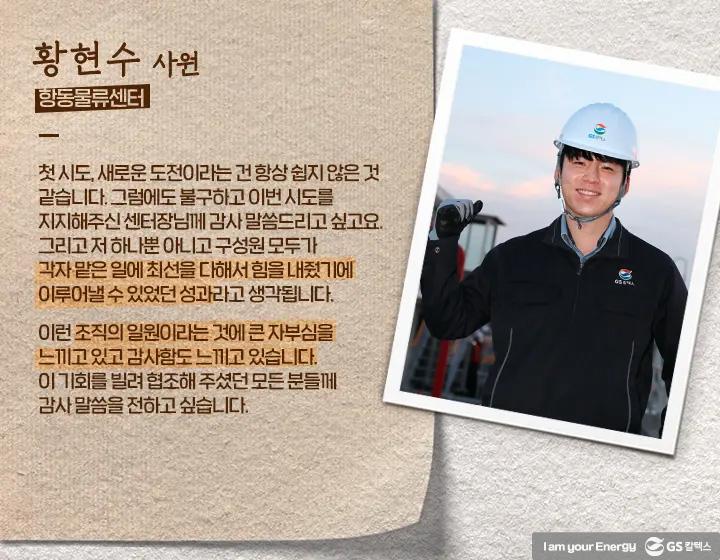
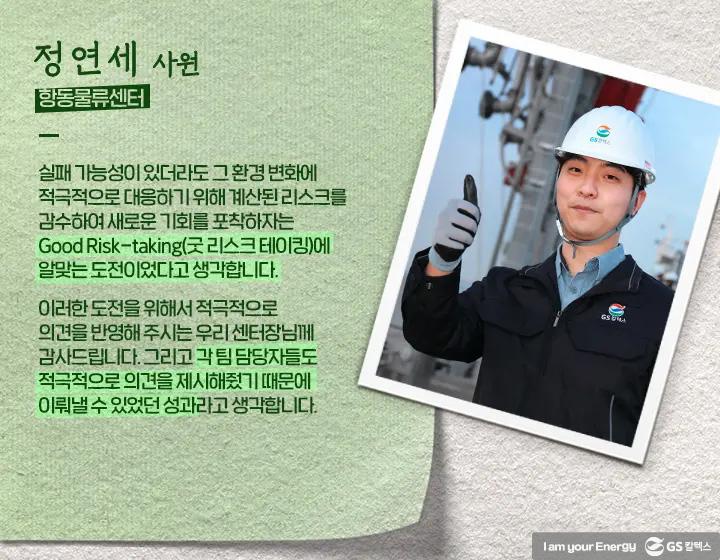
새로운 시도와 변화를 통해 개인과 회사가 함께 성장하고 있는 모습을 발견할 수 있었습니다. 변화에 대해 두려워하기보다 변화를 위한 방법을 적극적으로 고민했던 GS칼텍스 항동물류센터 구성원들에게 큰 박수를 보냅니다.
참고
* 로딩암(loading arm) : 석유화학제품을 하역하거나 선적할 때 사용되는 배관 설비