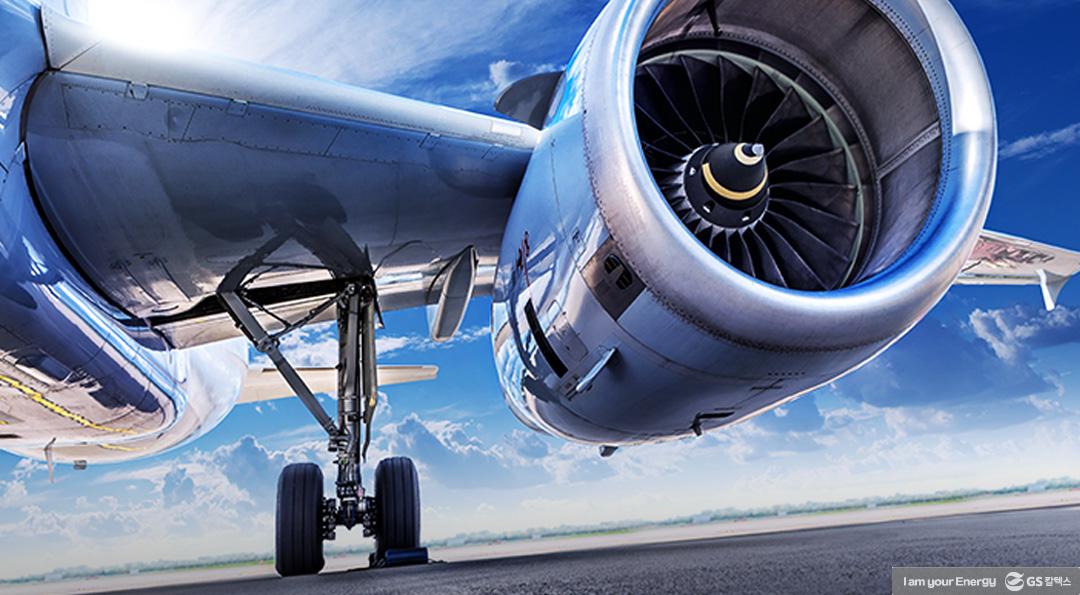
전통 제조 기업에서 디지털 제조업으로 성장
코로나19 이후 빠르게 변하는 디지털 시대를 맞아 DX(Digital Transformation, 디지털 트랜스포메이션)는 기업의 생존을 위한 필수 요건이 되었습니다. 인공지능(AI), 빅데이터, 사물인터넷(IoT), 블록체인, 클라우드 등 4차 산업 혁명 핵심 기술이 빠르게 발전하면서, 기업들은 기존과 다른 방식으로 고객, 프로세스, 서비스를 새롭게 정의하고 있죠. 지난번 소개해드린 ‘토요타’ 사례에 이어, 두 번째 DX 케이스는 끊임없이 디지털 혁신을 추구하는 131년된 스타트업, ‘제너럴 일렉트릭(GE)’입니다.
에디슨이 만든 기업 GE는 1892년 창립 이래 전구를 비롯해 냉장고, 세탁기 등의 가전 제품들을 만들어온 전통 제조 기업이지만, 2011년부터 ‘산업인터넷(IIoT)’, ‘프레딕스(Predix)’, ‘패스트웍스(Fastworks)’ 등 소프트웨어에 기반한 사업을 전개하는 ‘디지털 제조업’으로 성장하고 있습니다.
GE가 새롭게 제시하는 DX 혁신, 함께 살펴볼까요?
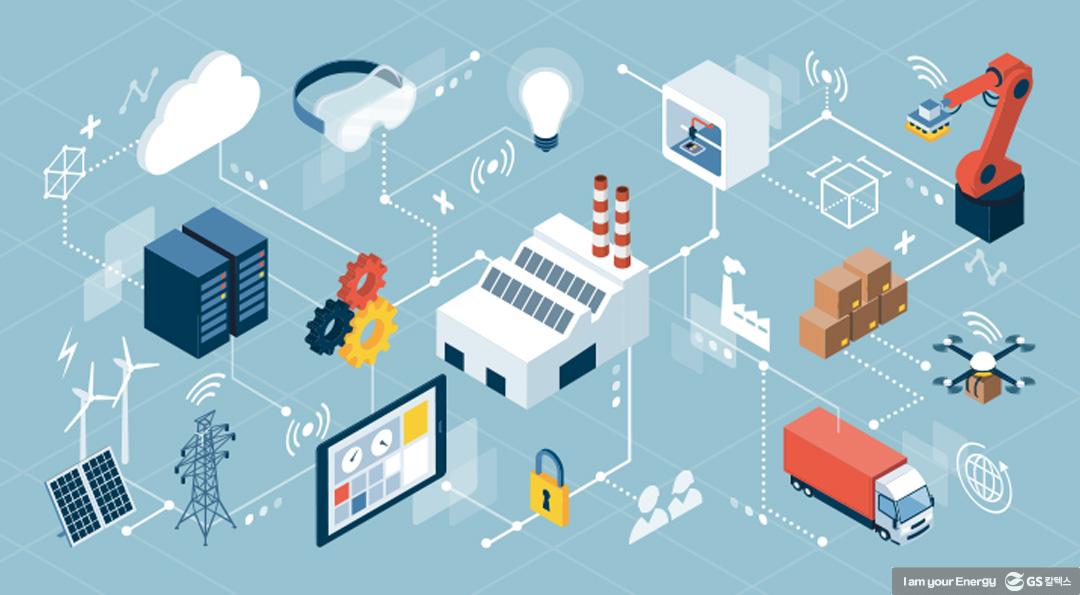
산업 현장의 기계 장비에 사물인터넷을 접목시킨 ‘산업인터넷’
항공기 엔진, 병원의 자기공명영상(MRI)장치, 발전소 가스터빈 등 산업 현장에서 사용하는 장비들은 방대하고 중요하며 복잡한 데이터들을 끊임없이 생성합니다. 하지만 이 데이터들은 대부분 적재적소에 사용되지 못하고 낭비되고 있었죠. GE는 나날이 복잡해지는 기계와 시스템 속에서 이와 같은 비효율성 문제를 ‘산업인터넷(IIoT)’ 소프트웨어로 해결하고자 했습니다.
산업인터넷을 적용한 기계는 스스로 데이터를 공유하고 분석한 뒤, 관련 정보를 엔지니어에게 전달합니다. 엔지니어는 이 데이터를 스마트 알고리즘에 입력하여 인사이트를 도출하고, 더 효율적인 의사결정 할 수 있습니다. 디지털 생태계를 구축해 기존 설비나 운영체계를 최적화하는 것입니다.
실제로 미국 항공사들은 GE의 산업인터넷 기반 항공기 지능형 유지보수 예측 시스템을 이용해 연간 6만회의 항공편 지연 및 취소를 방지했고, 미국 동부 최대 철도 운영회사인 노퍽 서던(Norfolk Southern)도 GE의 운행 최적화 시스템을 도입해 열차 속도를 10~20% 높이고 연료 사용을 약 6.3% 절감할 수 있게 되었다고 해요.
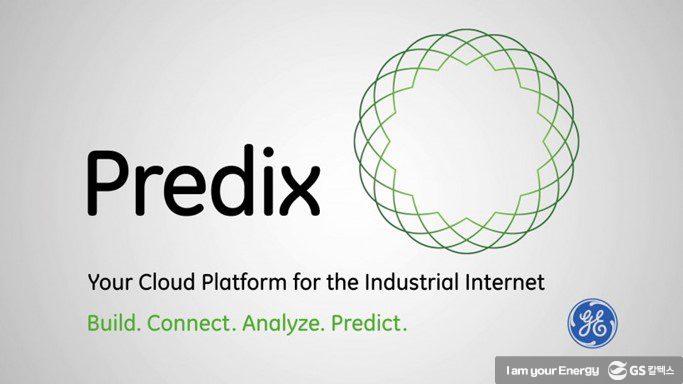
내∙외부 개발자 위한 산업용 클라우드 플랫폼 ‘프레딕스(Predix)’
GE는 2015년 세계 최초로 산업 클라우드 솔루션인 ‘프레딕스(Predix)’를 선보였습니다. 프레딕스는 산업 기계 및 설비에서 수집한 대규모 데이터를 분석하여 소프트웨어 개발을 지원하는 서비스형 플랫폼입니다. 구글의 안드로이드나 애플의 iOS처럼 빠르게 산업인터넷용 어플리케이션을 개발할 수 있도록 도와주죠.
특히 프레딕스가 클라우드 방식이라는 점에 주목해야합니다. 클라우드 방식은 엔지니어들이 장소와 시간의 제약을 받지 않고 데이터를 관리할 수 있게 지원해줍니다. 중공업의 데이터가 방대할지라도 현장에서 분석뿐 아니라, 예측, 통합 등의 가공도 바로 가능해지는 것입니다.
다만, 시행착오는 존재했습니다. 초기에 시장에 진입했고 데이터의 양도 워낙 많았기 때문이에요. GE는 모든 참여자가 데이터로부터 결과를 도출할 수 있게 지원하고자 했으나, 올바른 방식으로 클린 데이터를 확보하는 데 한계가 있음을 인정했습니다. 이를 위한 해결책으로 현재 GE는 ‘버티컬 마켓’으로 새롭게 피보팅(Pivoting)하며 특정 과제를 해결하고 성과를 이끌어내는 독자적인 애플리케이션을 개발하는데 초점을 두고 있습니다.
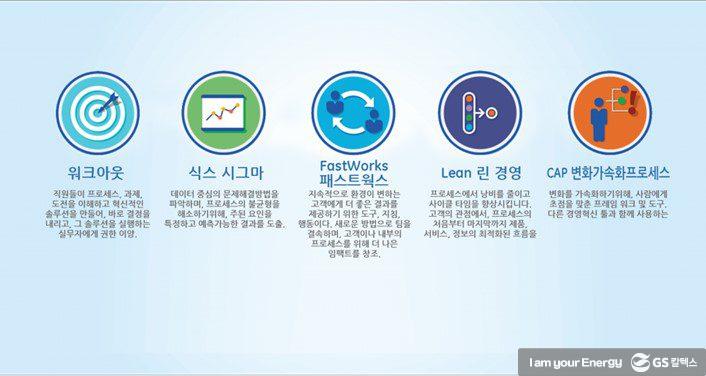
디지털 실행 조직 역량의 첫걸음, 고객 성과 달성 툴 ‘패스트웍스(FastWorks)’
GE는 제조업의 폐쇄적인 방식에서 벗어나, 고객의 요구를 빠르게 반영할 수 있는 스타트업 방식을 적용하고자 했습니다. DX가 성공하려면 기술의 변화보다 구성원들의 디지털 인지도 및 기업문화의 변화가 더 중요하기 때문이죠. 이를 위해 GE는 하드웨어 엔지니어들도 ‘패스트웍스(FastWorks)’ 툴을 이용하여 소프트웨어 업계의 ‘애자일(Agile) 개발’ 방식으로 일할 수 있도록 했습니다.
패스트웍스는 조직이 더 빠르게 품질을 개선하고 낭비를 줄이는 제조업의 ‘린 식스 시그마(Lean Six Sigma)’ 원칙에 실리콘밸리 기업들의 ‘린 스타트업 문화’를 결합하여 만들어졌습니다. 고객의 목소리를 빠르게 반영하고 수정하기 위해 실현가능 최소한의 제품(Minimum Viable Products, MVP)을 지향하죠. 작게 시작하고, 짧은 사이클로 개발을 진행해, 낭비없이 효율적으로 품질을 발전시키는 것입니다.
패스트웍스는 GE의 모든 사업 부분으로 확산되고 있습니다. 구축(Build)-측정(Measure)-학습(Learn)의 3단계의 프로세스를 통해 소형 제품뿐 아니라 대형 발전용 가스 터빈 등 전 과정에서 고객의 니즈에 초점을 두며 개발 비용을 줄이고 효율성을 향상시키고 있습니다.
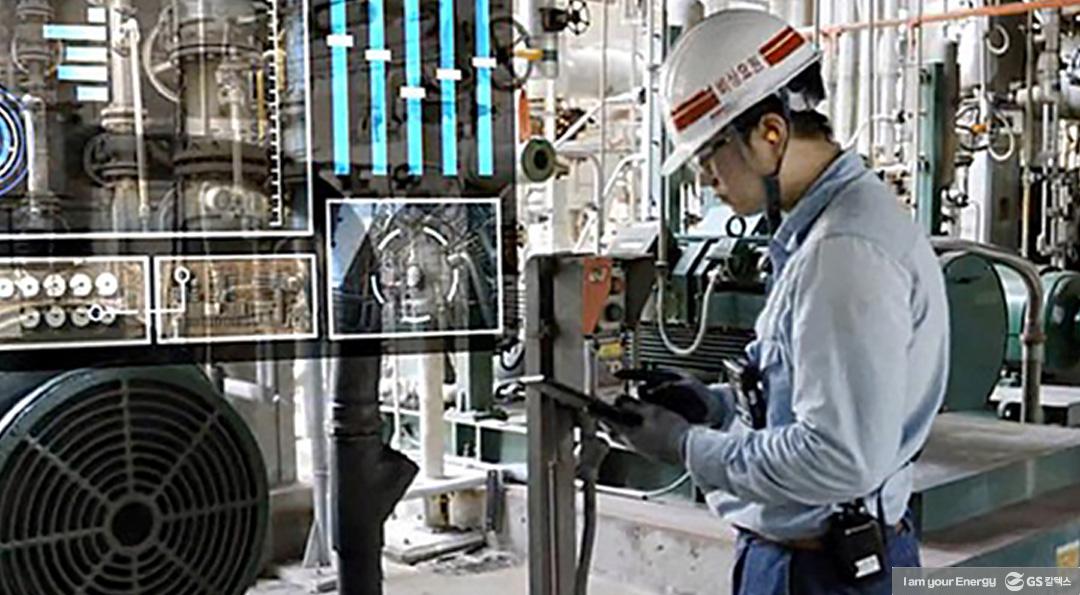
적극적인 DX 행보로 최적의 솔루션을 구축하는 GS칼텍스
앞서 살펴본 바와 같이 GE는 현장에서 생성되는 데이터의 중요성을 인지하고 디지털을 기반으로 한 다양한 소프트웨어 플랫폼을 만들며, 제조기업을 넘어 소프트웨어 기업으로 새로운 도약을 시도했습니다. 패스트웍스를 통해 기업 내부의 문화도 효율적으로 바꾸었죠.
GS칼텍스 기업의 생산성과 효율성을 높일 수 있는 디지털 전환을 가속화하고 있습니다. 공장 상황을 실시간으로 관리하며 손실을 최소화하는 ‘공장 통합 관제 시스템’과 함께, 변경사항이 발생했을 때 안전성을 미리 검증하고 가상환경에서 재현해 볼 수 있는 ‘디지털 트윈(Digital Twin)’ 인프라도 마련돼 있죠.
이외에도 GS칼텍스는 클라우드 서비스형 소프트웨어(Software-as-a-Service, Saas) 분석 플랫폼을 활용할 수 있는 산업인터넷 환경도 준비하고 있습니다. 이를 통해 수많은 공정 시스템 및 장비의 데이터를 취합해 가치 있는 정보를 신속하게 취득할 계획입니다.
GS칼텍스는 앞으로도 급변하는 미래 환경에 끊임없이 적극적으로 대응해 나갈 것입니다. GS칼텍스의 DX 여정과 지난 케이스 ‘토요타’의 DX 사례도 아래 글에서 더 자세히 살펴보세요!
- DAX, IIoT, 디지털 트랜스포메이션, 산업인터넷