- Inaugural Tech Exchange highlights the latest trends in digital technology
- CEO Saehong Hur: “A culture of employee-driven participation is key to digital transformation”
- Digital technologies at the Yeosu plant drive process optimization and enhanced safety management
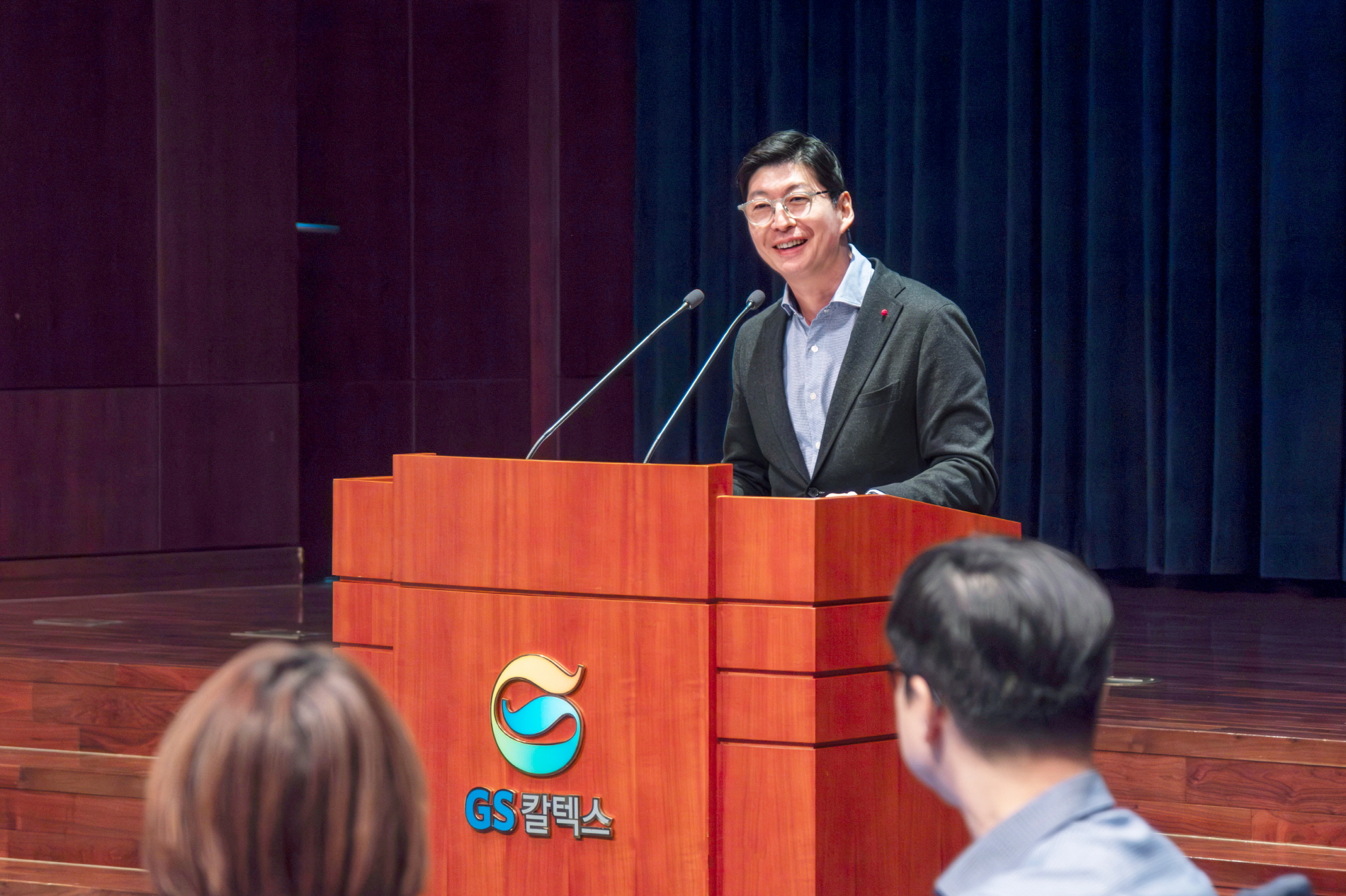
GS Caltex (CEO Saehong Hur) held its inaugural Tech Exchange on April 30 at GS Tower, its headquarters in Gangnam, Seoul. The event was organized to enhance employees’ capabilities in digital technology by showcasing the latest trends and practical applications while strengthening cross-functional collaboration and networking across the company.
Under the banner of Deep Transformation, GS Caltex continues to pursue sustainable and profitable growth. To that end, the company is actively driving Digital Transformation (DX) initiatives, applying digital technologies to its production sites to enhance manufacturing competitiveness and reshape the way employees work. GS Caltex is also fostering a culture of voluntary innovation by providing employees with diverse training and exchange opportunities to help them apply digital technologies in their daily work.
The Tech Exchange program, launched as part of these DX efforts, is designed to enhance employees’ understanding of digital technologies by introducing the latest trends. Covering a wide range of topics – including AI, robotics, mobility, cloud computing, and digital twin technologies – the program aims to inspire practical ideas and promote a culture of cross-functional collaboration across departments. Going forward, the Tech Exchange will be held regularly with industry experts sharing real-world application cases from a variety of sectors.
In this month’s inaugural Tech Exchange, Teddy Lee, CEO of Braincrew, delivered the keynote address titled “AI Agent Trends 2025.” Lee explained the principle of AI agents, which enables systems to understand user intentions, make autonomous decisions, and perform tasks independently. He further predicted that such proactive problem-solving AI agents will automate complex operations and lead the global market by 2025. The keynote was followed by a networking session where employees freely exchanged questions and insights across departments that previously had little interaction, and discussed the possibilities of applying AI agent technologies to real-world collaborations.
In addition to the Tech Exchange, GS Caltex is cultivating a pool of internal digital experts through its in-house training program, the Digital Academy, to analyze on-site problems using data and realize improvements through digital technologies. GS Caltex has operated annual programs such as business data analyst training and low-code developer training for building applications with minimal coding since 2023, and plans to expand its offerings to include generative AI training in 2025. To date, the company has produced more than 220 internal digital experts.
Moreover, GS Caltex CEO Saehong Hur has consistently emphasized that digital transformation should not be limited to a few specialists or departments, but must extend across the entire organization, driven by the willing participation of employees. Speaking at a recent workshop for executives, he stated, “A culture of employee-driven participation is the core competitiveness for sustainable growth,” adding, “Such a culture enables proactive adoption and practical use of digital technologies.” In keeping with his remarks, Hur regularly shares global best practices and the latest digital trends on internal communication channels to encourage employee interest and ongoing engagement in DX initiatives.
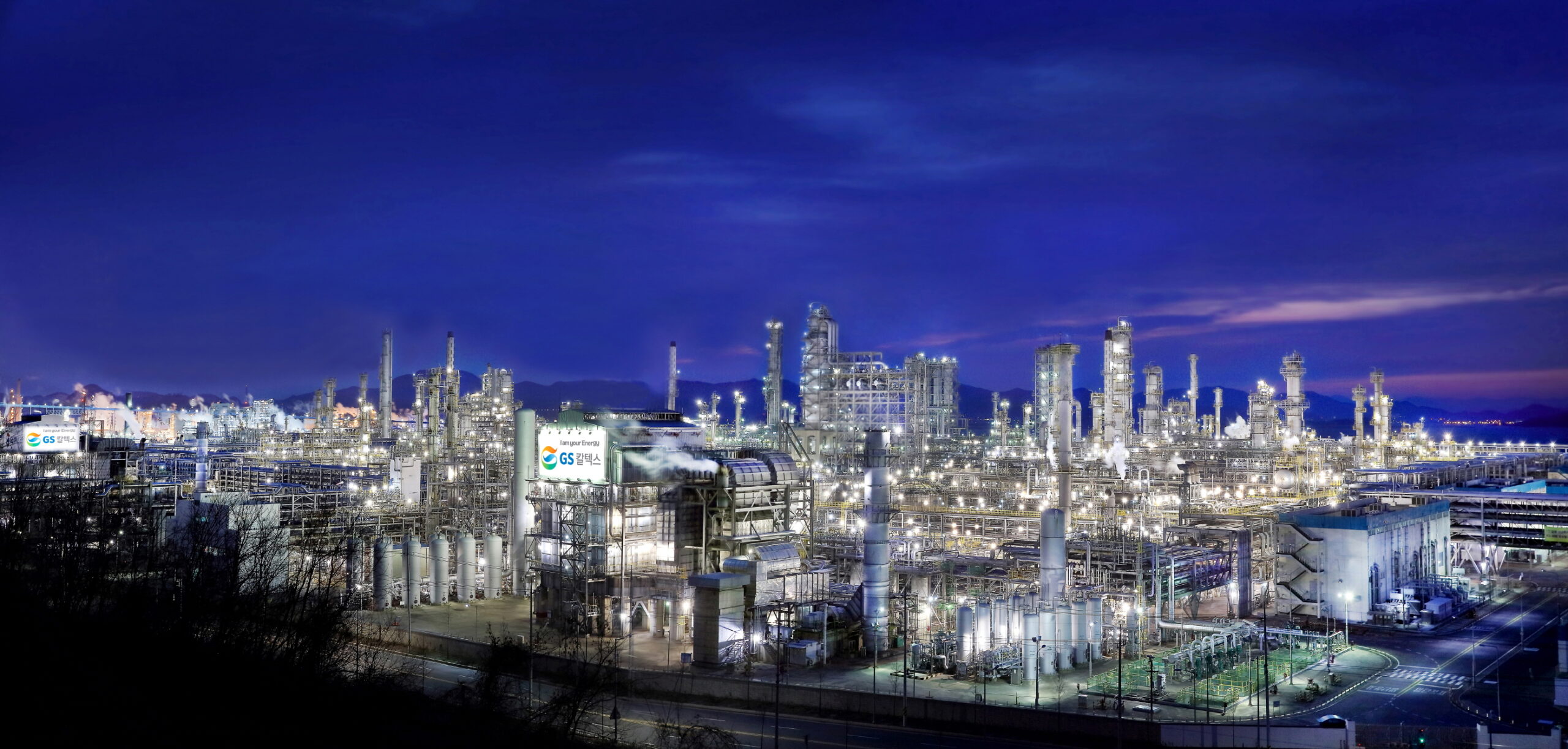
Building on the strength of senior management’s leadership and culture of employee participation, GS Caltex is identifying use cases and deploying digital technologies at its Yeosu plant, the core of its value chain.
The company’s growing portfolio of use cases takes a bottom-up approach in which the plant engineers, who best understand on-site operations leverage their understanding of digital technologies to rapidly identify pain points and implement practical solutions. Approximately 40 use cases were developed in 2023 and around 140 in 2024, leading to tangible improvements in areas such as process optimization and safety management at the Yeosu plant.
Specifically, GS Caltex has developed in-house AI models that optimize production processes by analyzing vast amounts of real-time data generated at the Yeosu plant. While past responses to process abnormalities relied largely on workers’ expertise and experience, AI models can now detect early warning signs and suggest real-time solutions. The models also predict product specifications based on real-time data and optimize operating conditions, contributing to an increase in the production of high-value-added products.
GS Caltex is further enhancing workplace safety and efficiency by deploying AI-based CCTV systems to detect potential hazards in real time and using drones and robots for inspections in high-risk areas, such as confined spaces and elevated sites. The company has also established a VR (virtual reality) and MR (mixed reality) simulation-based safety training facility where employees can train in work procedures and accident scenarios to reinforce safety awareness and help prevent accidents. GS Caltex also developed ‘AnGen Bot,’ a generative AI-based chatbot that offers fast and convenient access to safety guidelines so employees can stay focused on their tasks.
In recognition of its efforts, GS Caltex was selected as the anchor company for the petrochemical sector of the AI Autonomous Manufacturing Alliance under the Ministry of Trade, Industry and Energy (MOTIE) in July 2024 and received the Ministerial Award for its contributions to Korea’s industrial digital transformation in December 2024. The company also began leading MOTIE’s AI Autonomous Manufacturing Leading Project in September 2024 and is developing an autonomous AI manufacturing platform, accelerating its push to secure future competitiveness in digital manufacturing.